Temperature mapping
and validation services
Full service analysis and reporting for controlled environments and critical
storage areas
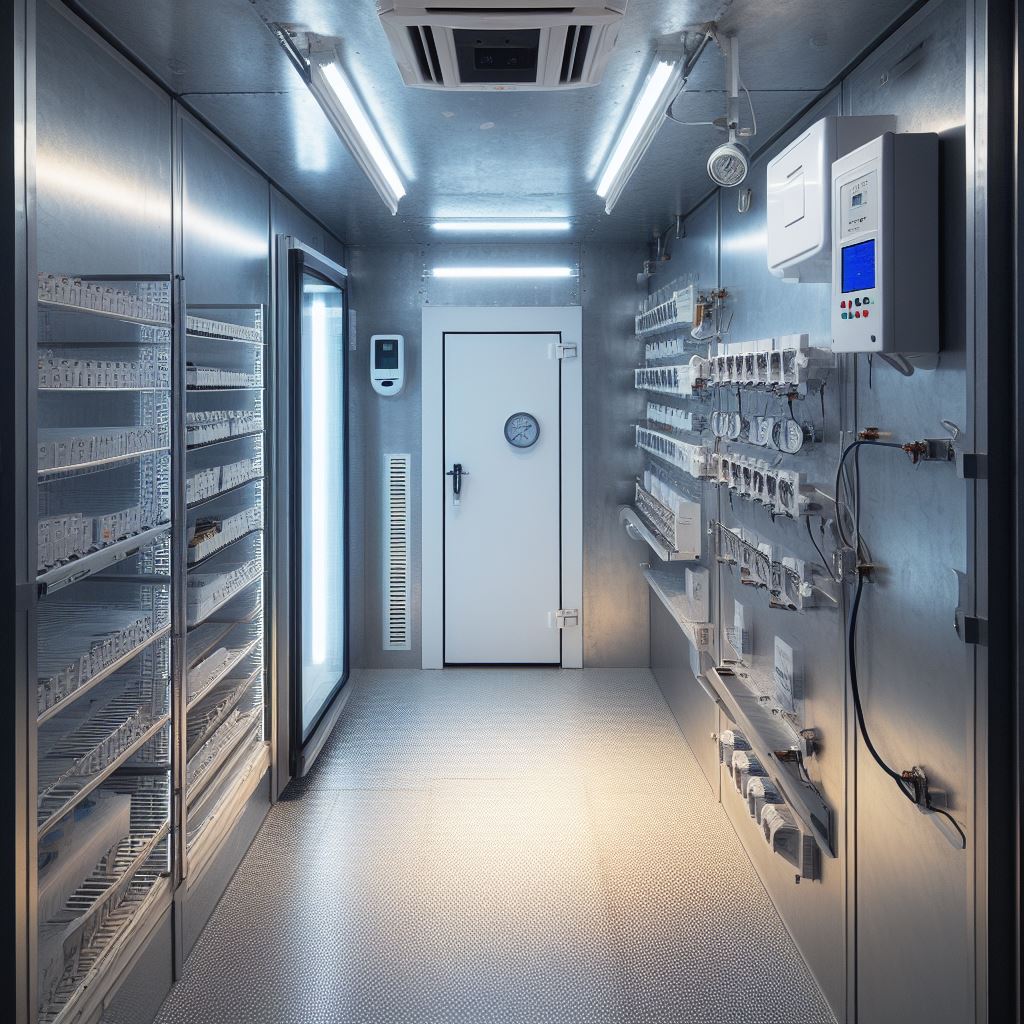
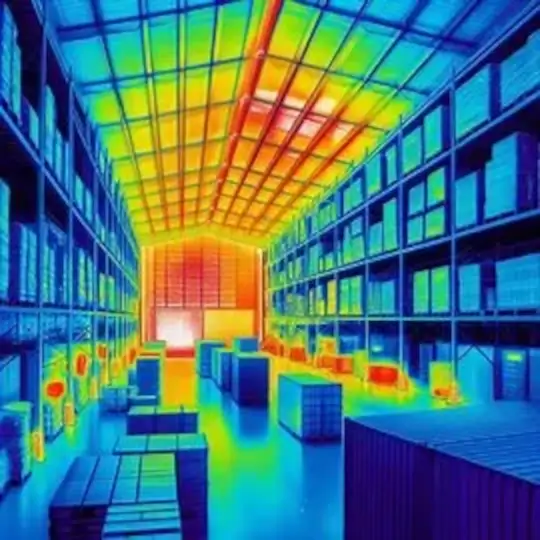
Temperature mapping and validation services
Temperature mapping is an important process for validating and documenting the temperature distribution within
equipment like coolers, autoclaves, and other systems that require consistent temperatures. By mapping
temperatures throughout the equipment, you can identify any hot or cold spots
that could impact your process or
products.
Paragon offers a full range of temperature mapping products and services to help our partners perform temperature mapping on their equipment, and ultimately meet regulatory or customer requirements with their processes. Temperature monitoring systems are available for both purchase and rental for customers wishing to perform their own mapping.
Our cGxP-qualified staff can also perform complete temperature mapping studies on your equipment on-site, and ultimately complete all validation documentation required.
Paragon offers a full range of temperature mapping products and services to help our partners perform temperature mapping on their equipment, and ultimately meet regulatory or customer requirements with their processes. Temperature monitoring systems are available for both purchase and rental for customers wishing to perform their own mapping.
Our cGxP-qualified staff can also perform complete temperature mapping studies on your equipment on-site, and ultimately complete all validation documentation required.
Service features
- Regulatory compliance: Ensuring compliance with industry regulations and standards such as FDA, GMP, GDP, and others.
- Data logging: Recording and storing temperature data over time for analysis, reporting, and compliance documentation.
- Risk assessment: Evaluating potential risks associated with temperature fluctuations and implementing measures to mitigate them.
- Customizable reporting: Generating customizable reports detailing temperature data, trends, and compliance status for internal records or regulatory submissions.
- Comprehensive monitoring: Optional continuous temperature monitoring solutions for cold and ambient storage areas, warehouses, and transportation vehicles. Systems includes real-time alerts and notifications of temperature breaches, allowing for immediate action to prevent product loss or damage.
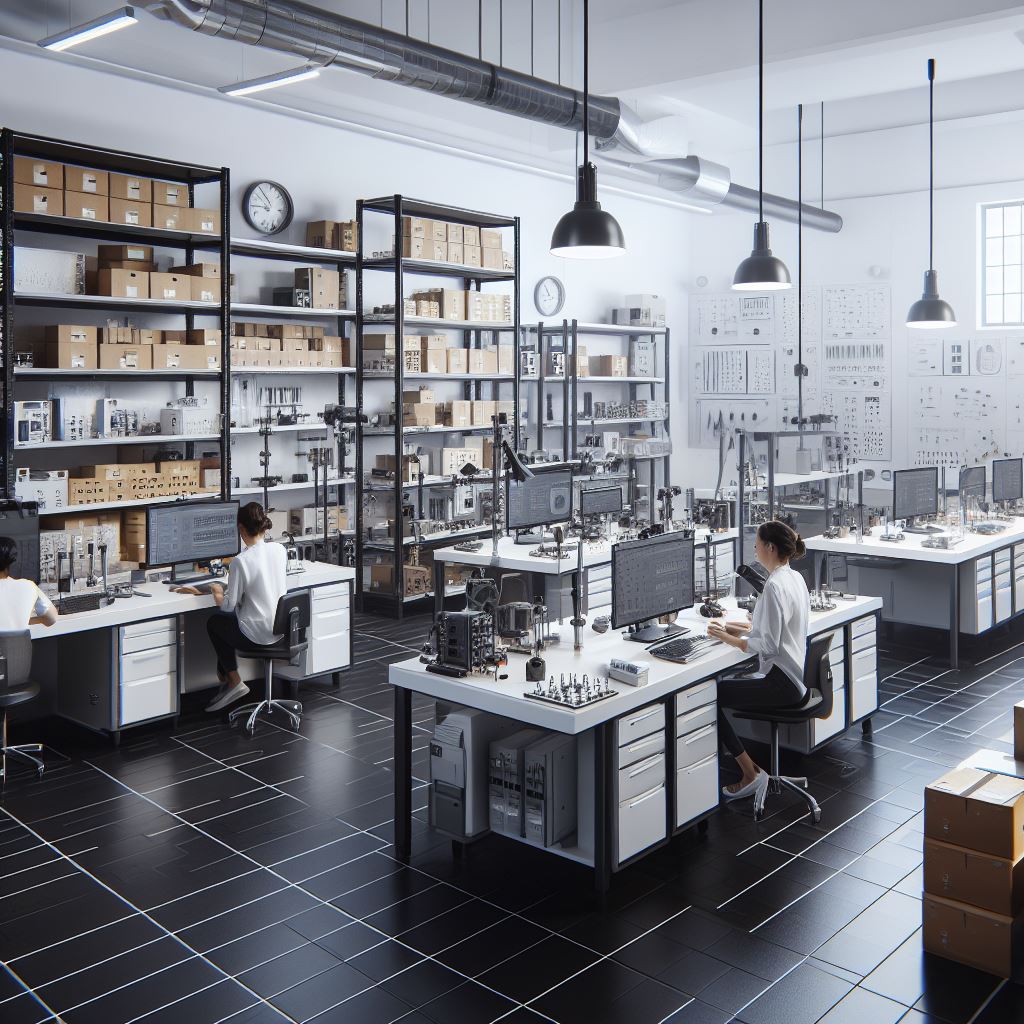
Site preparation
The temperature mapping process can be visualized in five distinct stages, starting with good preparation. Be
mindful of the following tasks for this stage:
- Obtain appropriate Paragon Robotics temperature mapping equipment like temperature probes (RTDs, thermistor or thermocouples), data loggers, and mapping software. Make sure equipment is calibrated and suitable for your expected temperature range.
- Review equipment datasheets and manuals to understand internal airflow and temperature control systems . Identify critical areas that will need careful mapping.
- Define your specific temperature mapping protocol including sensor locations, frequencies and duration of logging, environmental conditions, and operating parameters.
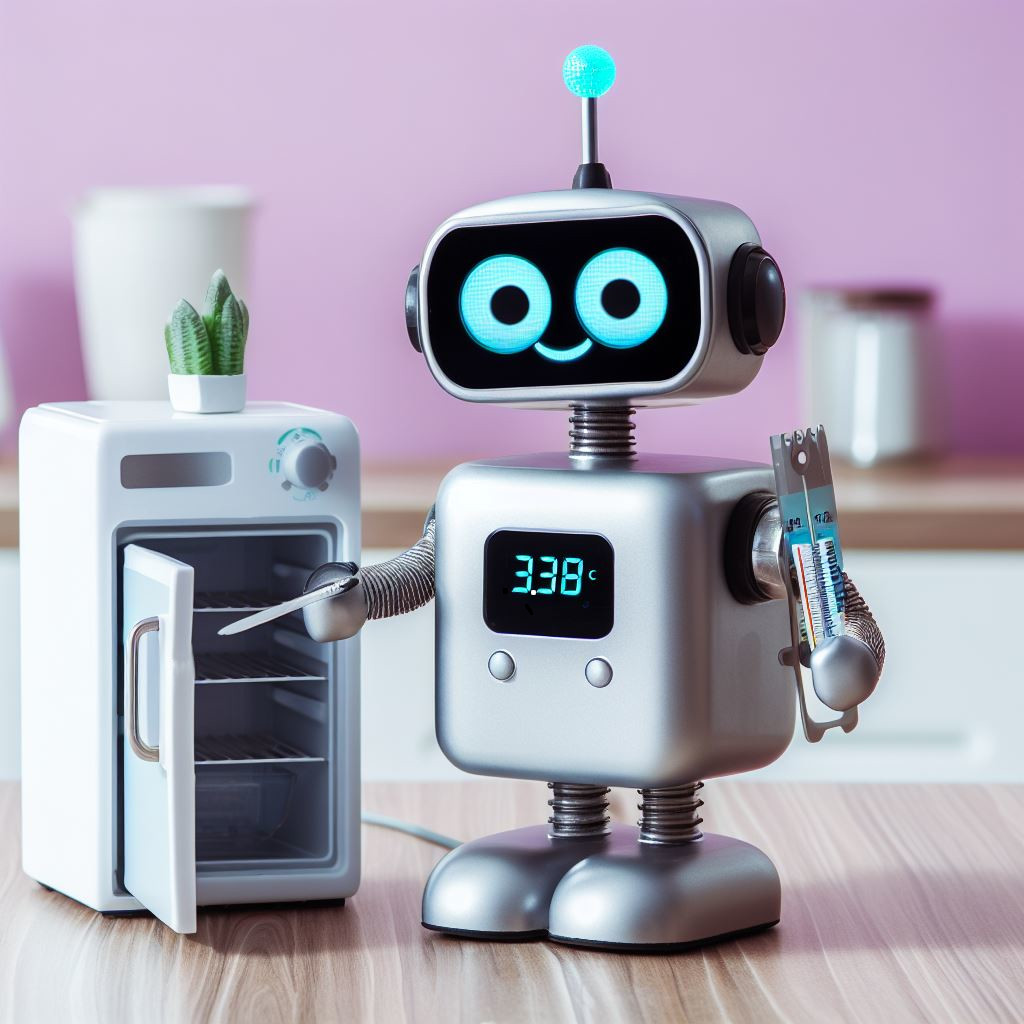
Sensor placement
Mapping requires a large number of measurement sensors. These can be purchased, rented, or provided by Paragon Robotics mapping service consultant. These sensors are typically removed after the mapping stage, and only a limited number of sensors may be permanently left in the equipment for long-term monitoring. When placing sensors:
- Strategically place temperature sensors throughout the equipment interior focusing on corners, edges, top, bottom, and known hot or cold spots.
- Sensors should be positioned in full contact with surfaces to get true readings . Use thermally conductive paste if needed.
- Be sure to map transitional areas like doors and openings . Have sensors trace expected product flow paths.
Mapping the area
Once the sensors have been placed, it's time to start the temperature mapping process. Duration and sample frequency will follow specific regulations or recommended temperature mapping guidelines to meet data requirements and capture thermal dynamics accurately:
- With area or equipment empty, run temperature mapping at required operating parameters for sufficient time to achieve steady state.
- For equipment with contents, map with worst-case product loads and distributions . Mapping may need to occur over full process cycle to access all variables.
- Log data frequently enough to capture thermal dynamics. Avoid unnecessary sensor movement.
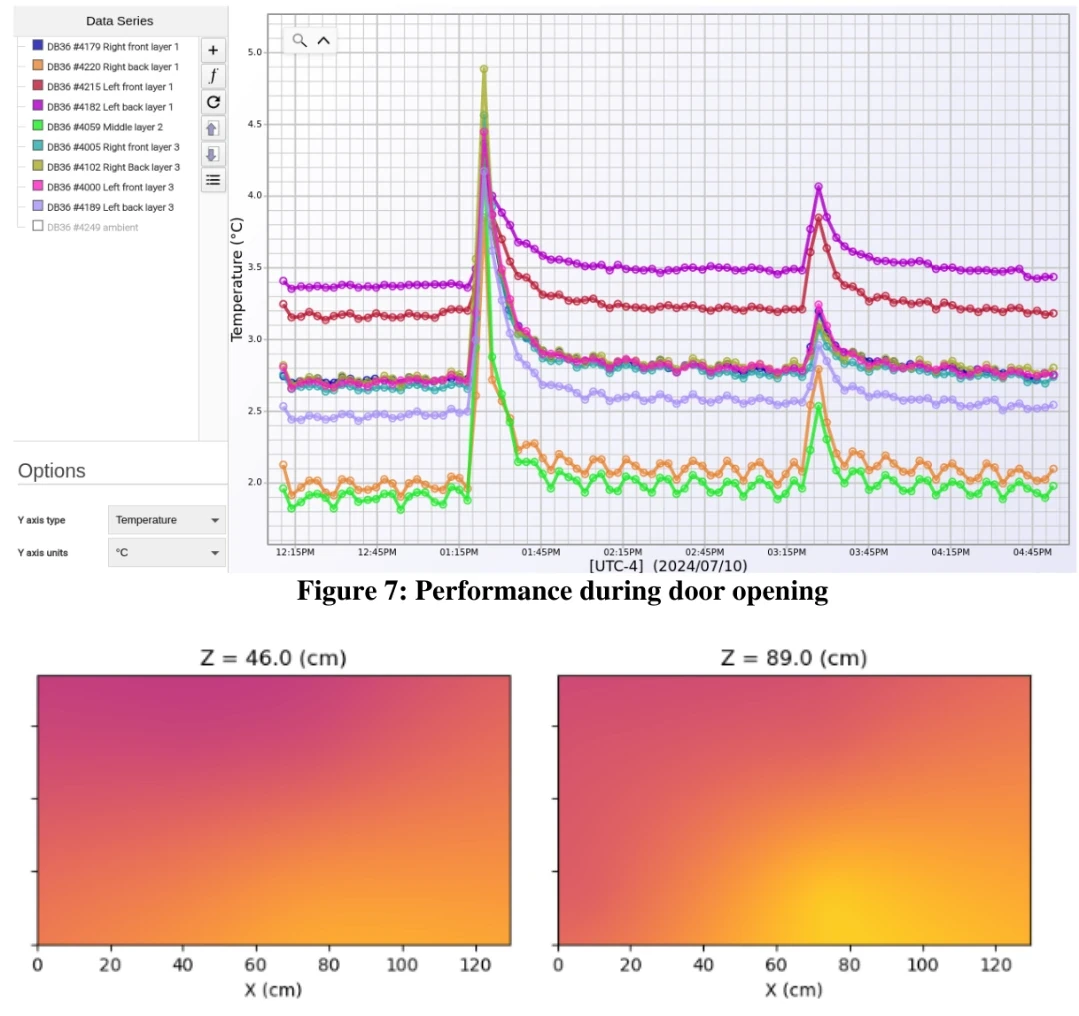
Data analysis
After the data is collected, the mapping sensors may be removed. If the analysis of the data can be performed
immediately, it may be best to delay removal of the sensors in case additional testing is needed later.
- Use mapping software to generate temperature distribution profiles and identify hot, cold, and transitional spots.
- Compare results to specified tolerances for equipment at required operational and performance qualifications.
- For out of spec variations, adjust controls or processes and remap to confirm improvements.
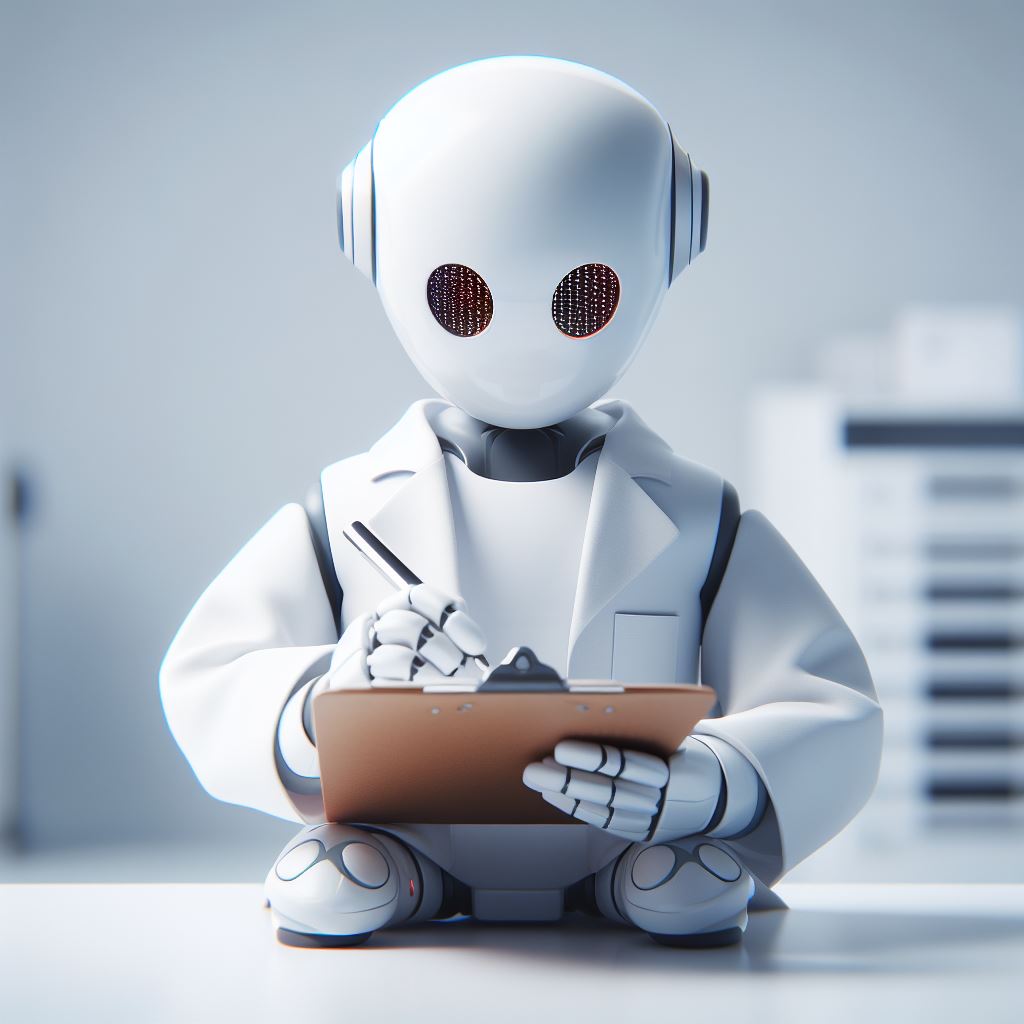
Quality/validation documentation
Most quality management systems or regulatory bodies will require thorough documentation
of the temperature
mapping. The documentation will often be reviewed by auditors, internal quality personnel, and even customer
quality managers, so be sure to create a high-quality document package using the following guidance:
- Report should detail methods, sensor locations, parameters, results, analysis, and verifications.
- Use charts, false-color maps, and diagrams to present temperature data clearly .
- Retain reports as evidence of proper installation and operation per processes.
Full-service temperature mapping
For cGMP regulated processes, temperature mapping is commonly part of the Operational Qualification (OQ) step
when commissioning new equipment. Regular remapping should also occur after repairs, adjustments, or process
changes. With careful temperature mapping, you can improve equipment uniformity, product quality, and regulatory
compliance
.
Paragon can support customers throughout the temperature mapping process, ranging from providing plug-and-play monitoring equipment for the activity, to turnkey on-site mapping services for product commissioning or re-commissioning. As a cGMP regulated manufacturer ourselves , we have significant experience within our quality department to help assist customers with qualification activities such as temperature mapping.
Paragon can support customers throughout the temperature mapping process, ranging from providing plug-and-play monitoring equipment for the activity, to turnkey on-site mapping services for product commissioning or re-commissioning. As a cGMP regulated manufacturer ourselves , we have significant experience within our quality department to help assist customers with qualification activities such as temperature mapping.