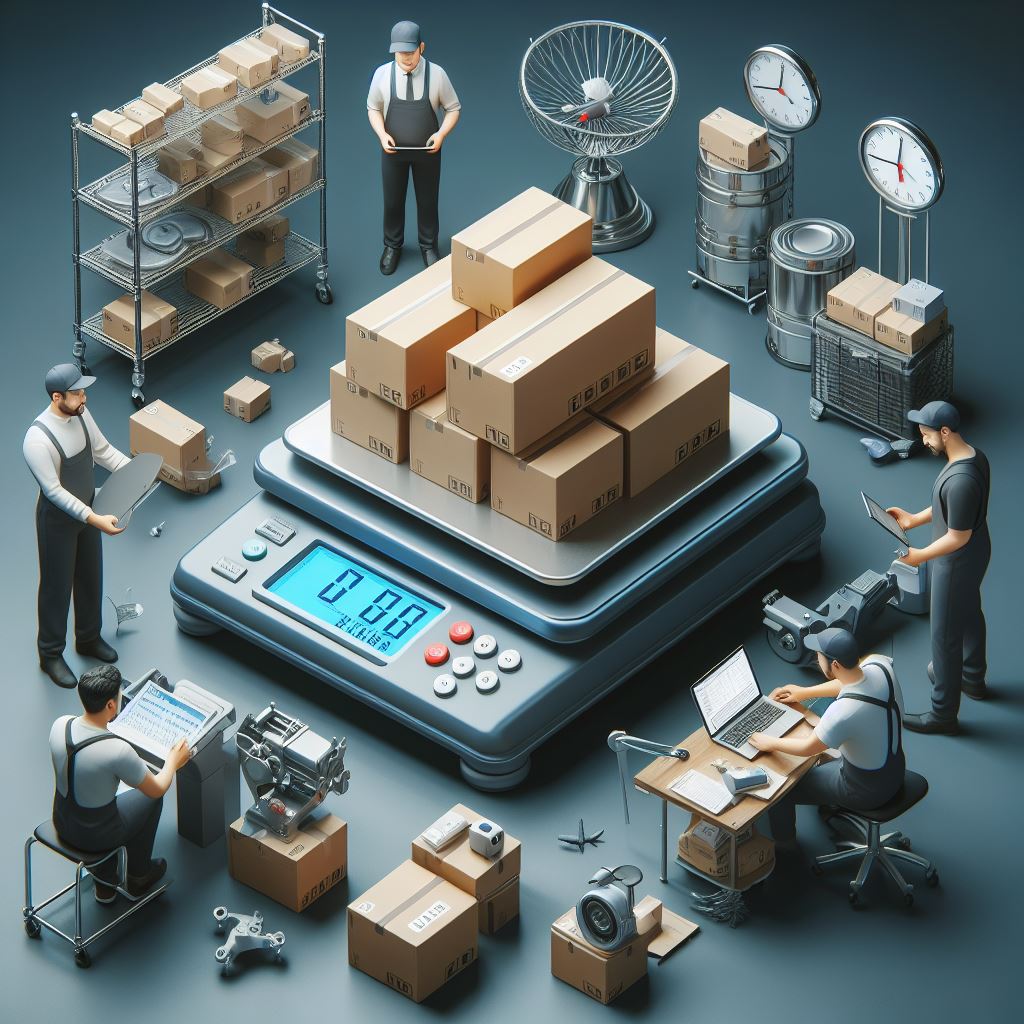
Vendor Managed Inventory (VMI) is a collaborative inventory management practice that has gained significant traction in modern supply chain management. In a VMI model, the supplier takes full responsibility for maintaining an agreed inventory of the customer's stock. This innovative approach shifts the traditional burden of inventory management from the buyer to the seller, creating a symbiotic relationship that can lead to improved efficiency, reduced costs, and enhanced customer service.
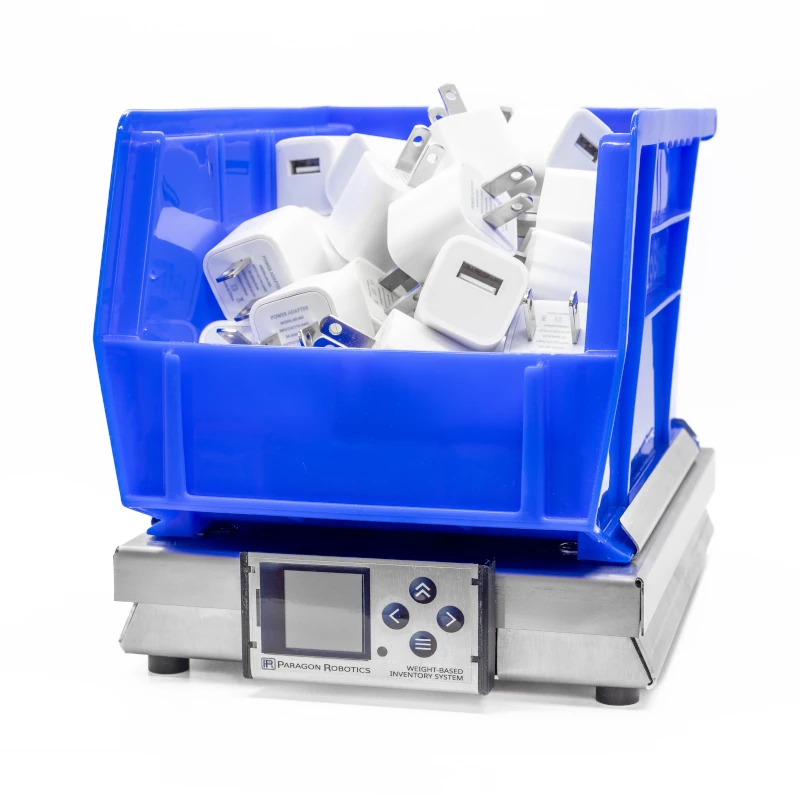
How VMI Works
In a VMI system, the vendor monitors the customer's inventory levels, often through real-time data sharing or regular reports. Based on this information, along with historical data and forecasts, the vendor makes decisions about when to replenish stock and in what quantities. The customer typically sets certain parameters, such as minimum and maximum stock levels, but the day-to-day management of inventory becomes the vendor's responsibility. This process often involves sophisticated inventory management software and analytics tools to ensure optimal stock levels are maintained.
Benefits of VMI
The implementation of a VMI system can bring substantial benefits to both the vendor and the customer:
- Reduced Inventory Costs - By optimizing stock levels, VMI can significantly reduce inventory holding costs for the customer.
- Improved Cash Flow - Lower inventory levels mean less capital tied up in stock, improving cash flow for the customer.
- Enhanced Supply Chain Visibility - VMI requires close collaboration and data sharing, leading to greater transparency across the supply chain.
- Reduction in Stockouts and Overstocks - With the vendor closely monitoring inventory levels, the risks of both stockouts and excess inventory are minimized.
- Streamlined Operations - VMI can reduce the administrative burden on the customer, allowing them to focus on core business activities.
- Better Forecasting - Vendors gain valuable insights into demand patterns, enabling more accurate forecasting and production planning.
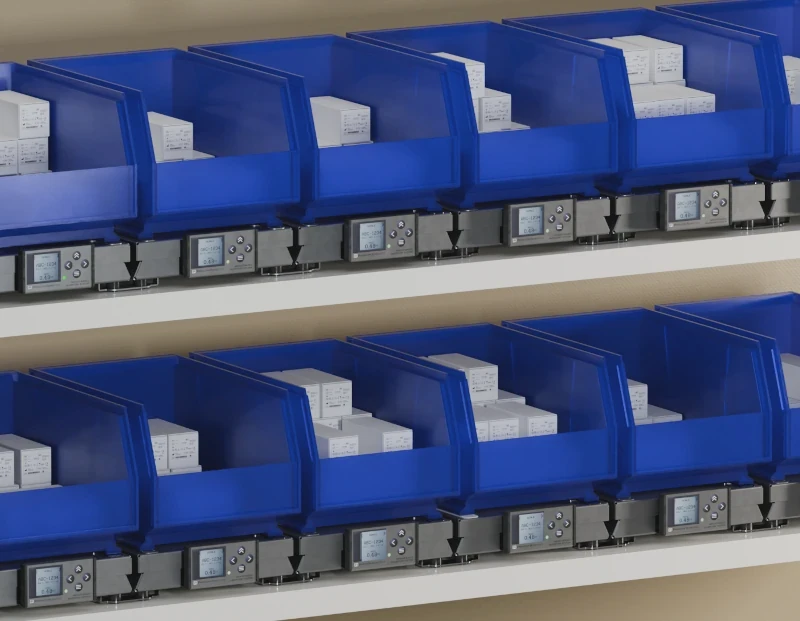
Challenges and Considerations
While VMI offers numerous advantages, it's not without its challenges. Successful implementation requires:
- Trust and Collaboration - Both parties must be willing to share data and work closely together.
- Technology Infrastructure - Effective VMI often requires investment in robust inventory management and data sharing systems.
- Clear Performance Metrics - Establishing and monitoring key performance indicators (KPIs) is crucial to ensure the VMI program is meeting its objectives.
- Cultural Shift - Both organizations may need to adapt their processes and mindset to fully embrace the VMI model.
VMI in Practice
VMI has been successfully implemented across various industries, from retail to manufacturing. For example, in the retail sector, many large retailers use VMI with their suppliers for fast-moving consumer goods. In manufacturing, VMI is often used for managing raw materials and components. The healthcare industry has also adopted VMI for managing medical supplies in hospitals, ensuring critical items are always in stock without tying up excessive capital.
As supply chains become increasingly complex and global, VMI continues to evolve. Advanced analytics, artificial intelligence, and Internet of Things (IoT) technologies are being integrated into VMI systems, allowing for even more precise inventory management and predictive capabilities. This ongoing innovation ensures that VMI remains a relevant and powerful tool in modern supply chain management, helping businesses stay competitive in an ever-changing marketplace.