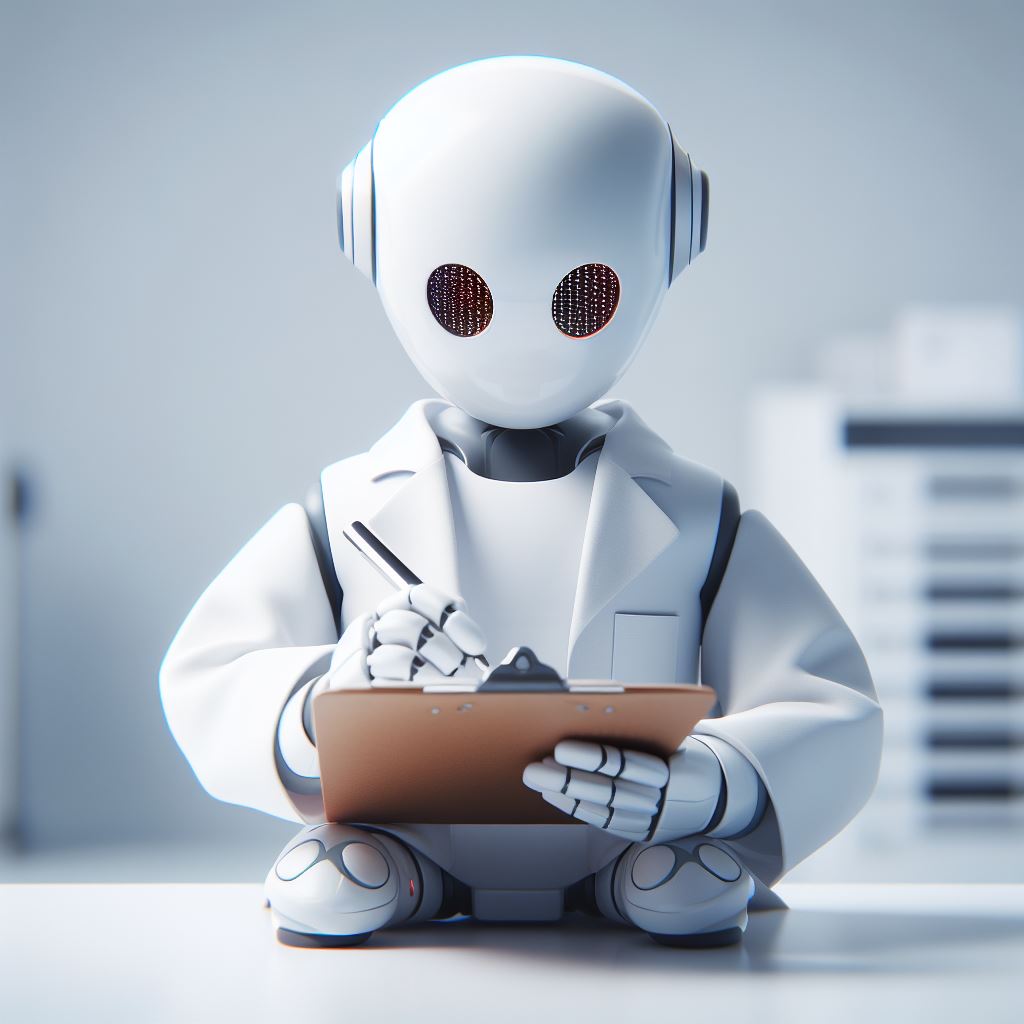
In pharmaceutical and biotech manufacturing facilities regulated under current Good Manufacturing Practices (cGMPs), all equipment must be validated to ensure it consistently operates within established parameters and specifications. Validation of process equipment used in other industries should also be validated before use, however a different methodology may be used for those applications.
The three main phases of equipment validation are Installation Qualification (IQ), Operational Qualification (OQ), and Performance Qualification (PQ). These three phases attempt to break up the commissioning process into stages, however many installations may combine phases due to the nature of the specific setup.
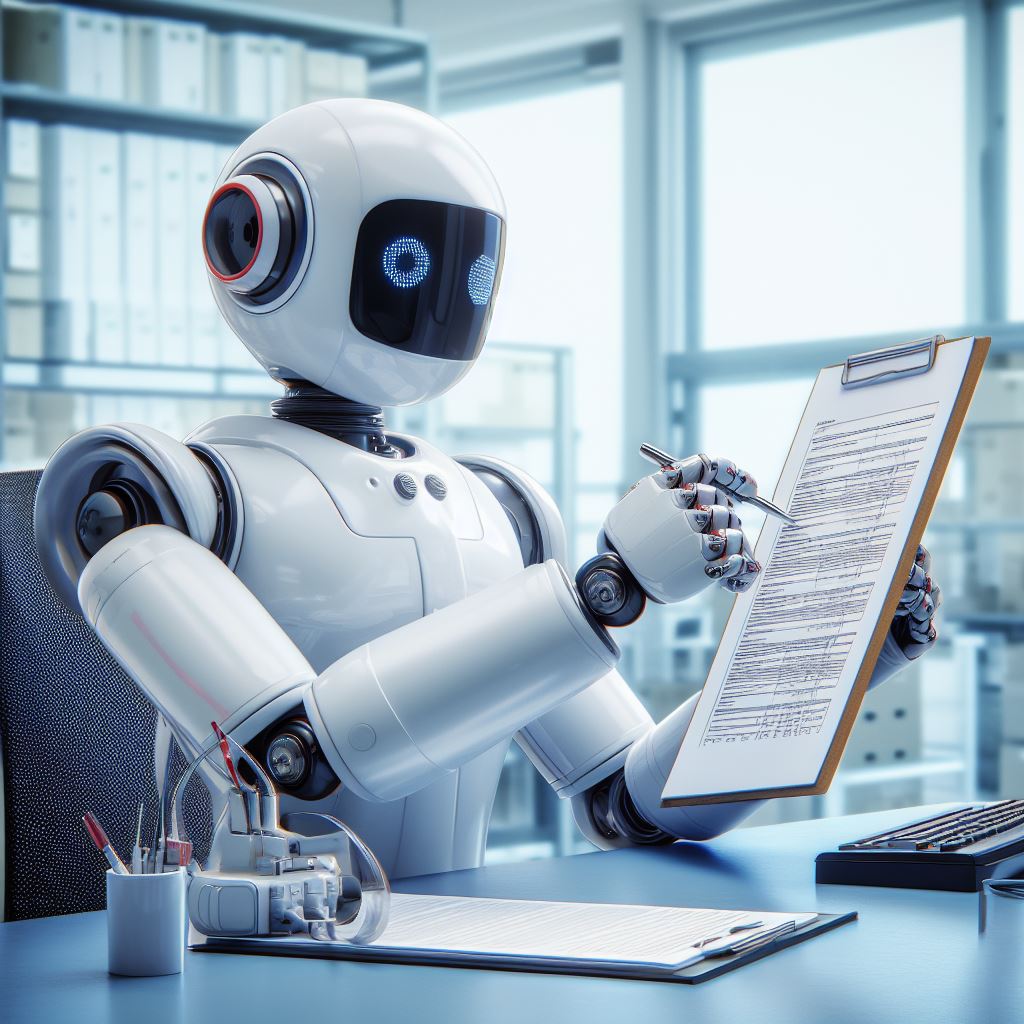
Installation Qualification (IQ)
IQ confirms that the equipment and systems have been properly installed per the vendor's instructions and specifications. It verifies that all components, utilities, and documentation provided by the vendor are correct and complete. In other words, it confirms the installer followed all the instructions from the original equipment manufacturer (OEM). IQ checks should include:
- All parts, modules, and accessories listed on the packing slip have been received
- User manuals, SOPs, calibration certificates, and other vendor documentation is stored and available
- Utilities like power, water, compressed air etc. are connected correctly and are functioning
- Equipment has been installed properly at the designated location
- Safety features like E-stops and interlocks are working
- Any system checks prescribed by the OEM have been performed and pass
IQ qualification should be performed by a skilled technician which is familiar with electrical, mechanical, plumbing, and other areas of equipment setup.
Operational Qualification (OQ)
OQ confirms that the installed equipment and systems operate as intended across their specified operating ranges. It verifies the equipment functions according to operational specifications when operated manually or automatically. OQ checks should include:
- Equipment can be started up and shut down properly
- Automated sequences and control systems function accurately
- Alarms and interlocks activate at appropriate set points
- Any process equipment meets critical performance attributes like temperature uniformity
- Performance mapping (for example mapping of temperatures at multiple points within a large cooler) shows that all requirements are met for all product being processed
OQ qualification should be performed by a skilled technician, which is ideally experienced with the process being commissioned. For example, if the equipment is a walk-in cooler, the technician should understand operational controls of a cooler, airflow within the cooler, and other details of the equipment operation.
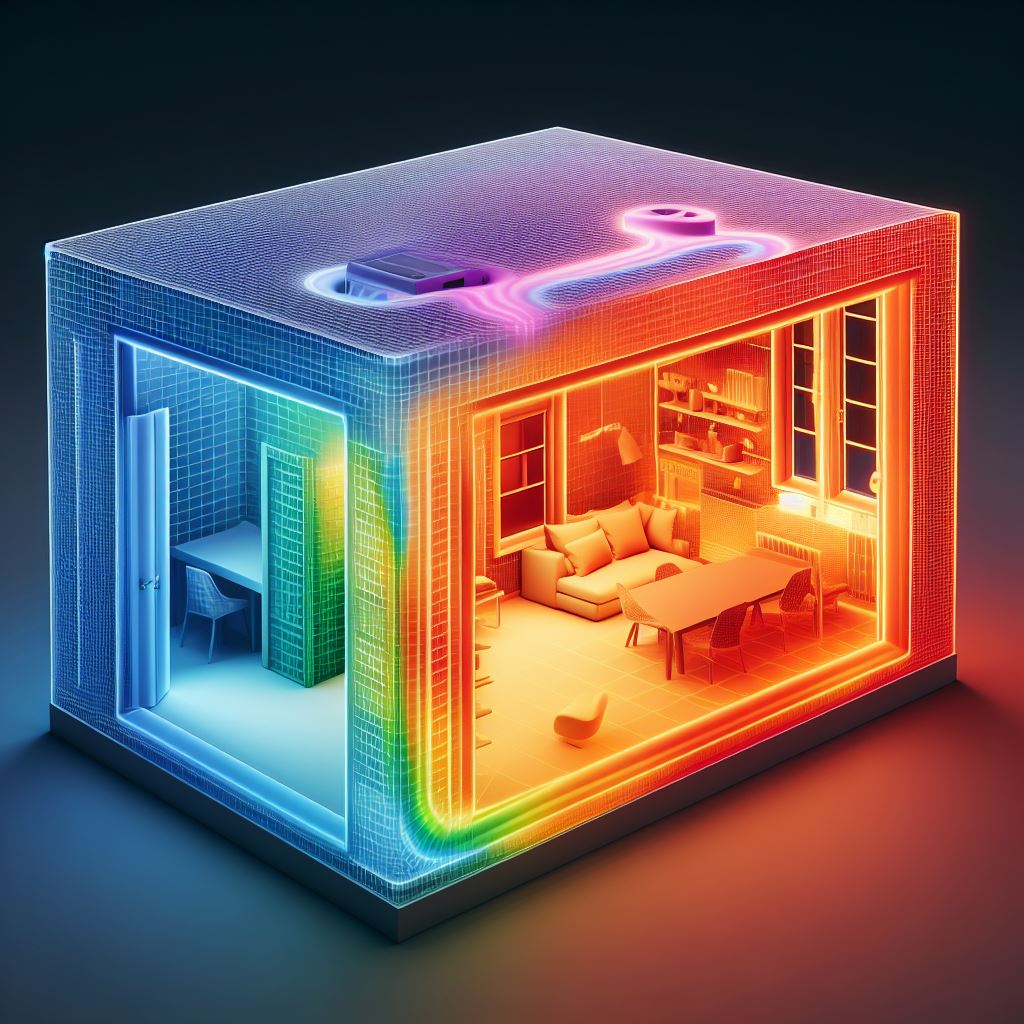
Performance Qualification (PQ)
PQ confirms that the equipment operates consistently and reproducibly when performing its intended function using product or representative materials. It determines that the equipment meets established acceptance criteria when operating under simulated or actual manufacturing conditions. PQ checks should include:
- Equipment meets quality attributes of final product under real or simulated conditions
- Monitoring controls like temperature, pressure sensors produce data meeting specifications
- Final process outputs and data are within expected ranges throughout entire process runs
- Analysis of the equipment performance is done over extended times (or continuously) to understand the stability of the equipment performance under various conditions
Since PQ qualification may require longer process runs to establish performance, it is many times performed by an internal quality group or third party service based on recorded data. Although this data can come from built-in sensors within the equipment, if possible it is best to monitor via additional monitoring system equipment.
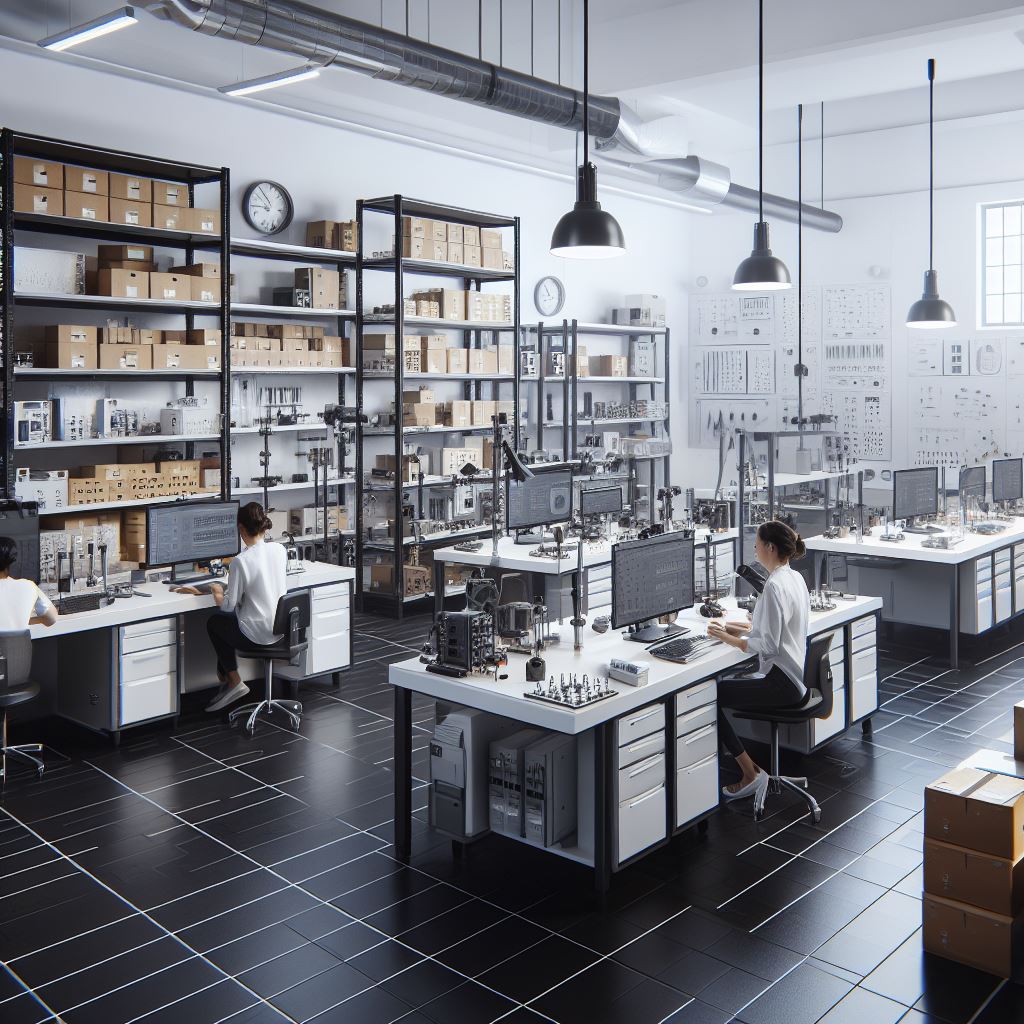
Conclusion
By executing a thorough IQ/OQ/PQ validation program, pharmaceutical companies can ensure equipment is installed, operating, and performing according to specifications required for cGMP processes. This provides documented evidence of suitability and minimizes quality risks when equipment is deployed for routine manufacturing.
Paragon can support customers throughout the IQ/OQ/PQ validation process, ranging from providing plug-and-play monitoring equipment for the process, to turnkey on-site validation services for product commissioning or re-commissioning.