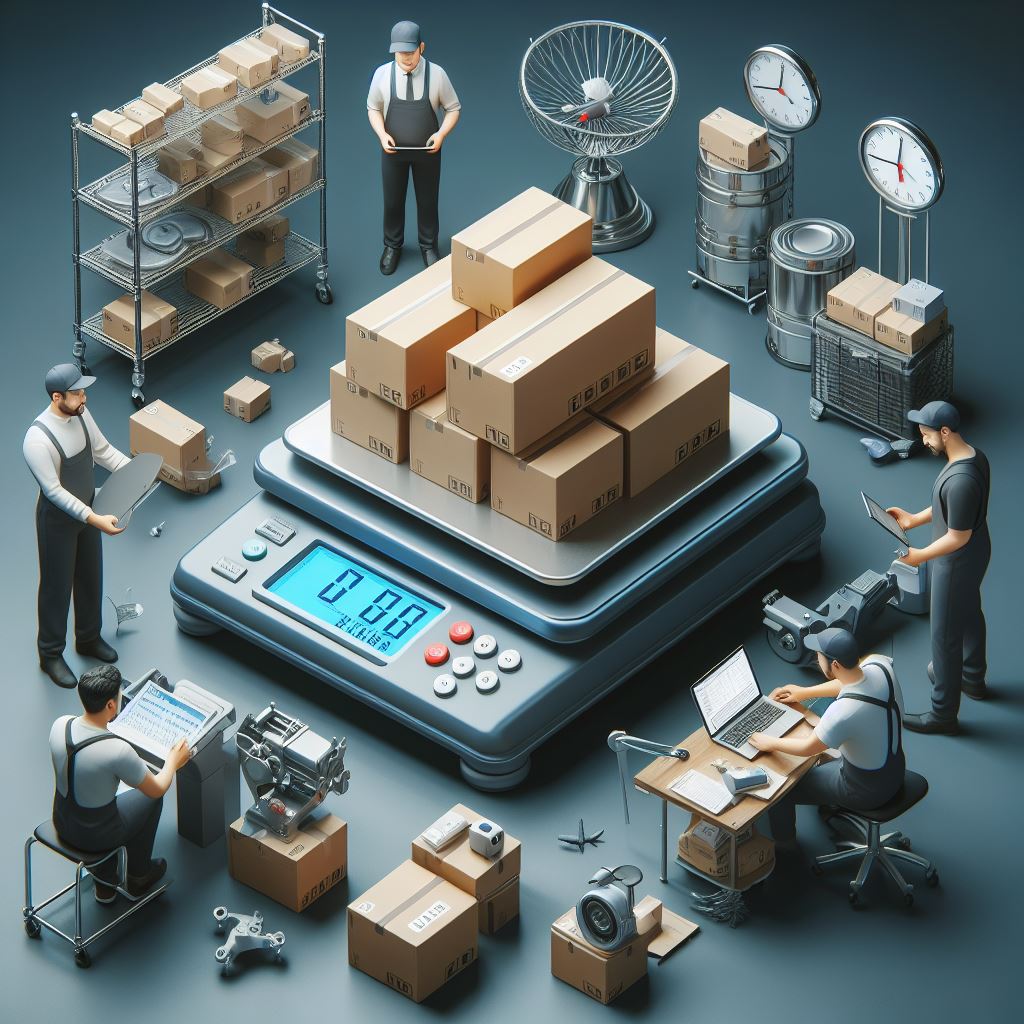
Load cells are crucial components in various industries, serving as the foundation for accurate weight and force measurements. These devices, particularly strain gauge-based load cells, play a vital role in applications ranging from industrial scales and material testing to aerospace engineering and medical equipment. Understanding how load cells work is essential for anyone involved in fields requiring precise force measurement.
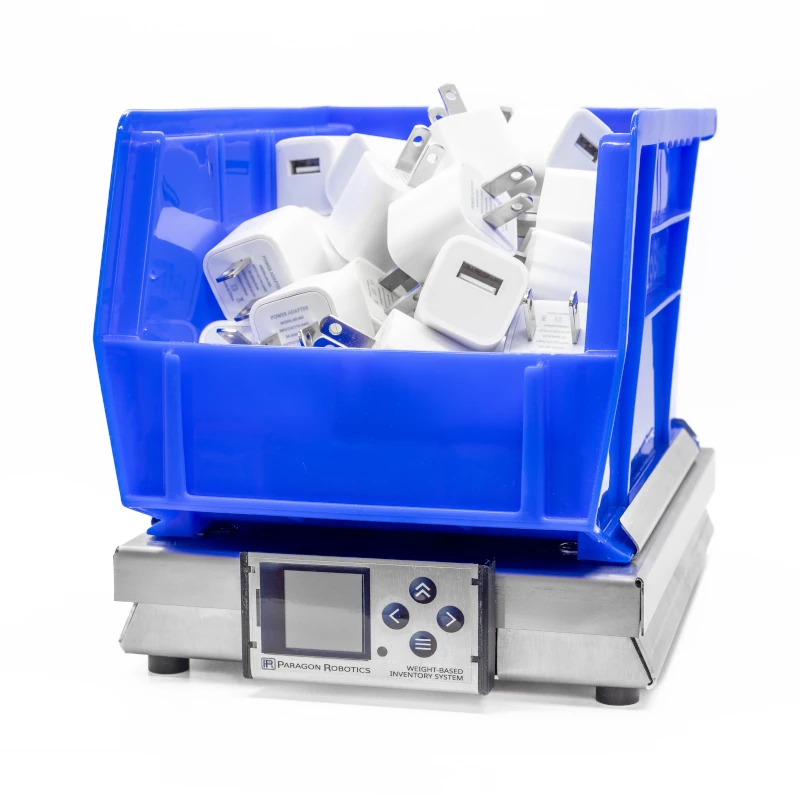
What is a Load Cell?
A load cell is a transducer that converts a mechanical force or weight into an electrical signal. While there are several types of load cells, including hydraulic, pneumatic, and capacitive, strain gauge-based load cells are the most common due to their accuracy, reliability, and cost-effectiveness. These load cells utilize the principle of electrical resistance changing in proportion to the applied force.
The Strain Gauge: The Heart of Modern Load Cells
At the core of a strain gauge load cell is the strain gauge itself – a thin, flexible metal foil or semiconductor material with a specific pattern. When a force is applied to the load cell, the strain gauge deforms slightly, causing a change in its electrical resistance. This change is directly proportional to the applied force, allowing for precise measurement.
How Strain Gauge Load Cells Work
- Force Application - When a force is applied to the load cell, it causes a slight deformation in the cell's body, typically made of metal.
- Strain Gauge Deformation - This deformation is transferred to the strain gauges bonded to the load cell body. As the gauges stretch or compress, their electrical resistance changes.
- Wheatstone Bridge - Most load cells use four strain gauges arranged in a Wheatstone bridge circuit. This configuration amplifies the small resistance changes and helps compensate for temperature effects.
- Electrical Output - The Wheatstone bridge converts the resistance change into a voltage difference. This voltage is typically in the millivolt range and is proportional to the applied force.
- Signal Conditioning - The small voltage signal is then amplified and may be converted to a standardized output (e.g., 4-20mA or 0-10V) for easy integration with control and display systems.
Applications and Advantages
Strain gauge load cells find applications in diverse fields due to their numerous advantages:
- High Accuracy - They can measure forces with precision, often within 0.03% to 0.25% of full scale.
- Versatility - Load cells can be designed for a wide range of capacities, from a few grams to hundreds of tons.
- Durability - When properly designed and installed, load cells can withstand millions of load cycles.
- Temperature Compensation - Modern load cells often include temperature compensation, ensuring accuracy across varying environmental conditions.
- Digital Integration - Many load cells now offer digital outputs, allowing for easy integration with computer systems and IoT devices.
From weighing ingredients in food production to ensuring the safety of heavy machinery, strain gauge load cells continue to be indispensable tools in our increasingly precise and automated world. As technology advances, these devices are becoming even more accurate, durable, and integrated into smart systems, further expanding their applications across industries.